わたしたちがつくるタイル、そのつくっている現場の日常を、写真、動画を交えながらご紹介しています。
今回工場でみてきたのは、「土練機」を使ってつくる湿式製法タイルの成形作業。
土練機=どれんき、と読みますが文字通り土を練る機械。空気を抜きながら土を練り、板状に粘土を押し出してタイルの形にする機械です。
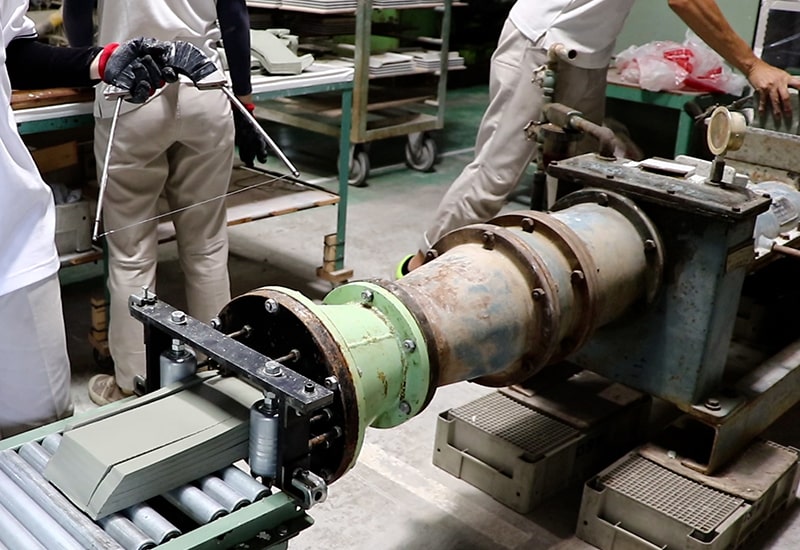
私たちの工場でつくるタイルのほとんどは「乾式製法」なのですが、もうひとつ、この真空土練機を使った「湿式製法」のものがあります。
▼ 乾式製法での成形の様子は、こちらの第2回「成形編」をどうぞ
https://tile-park.com/blog/detail/27124
乾式製法は、水分を飛ばしてサラサラの顆粒状の原料を、プレス機でギュッと押し固める製法です。焼成後の寸法精度も高く品質も安定しており、比較的低コストで大量生産が可能となります。
一方の湿式製法は、水分を含んだ「粘土」の状態から成形をおこないます。基本的にはこの土練機を使いますが、手で粘土を捏ねたり切り出したりといった成形方法も湿式製法になります。
上の写真は、土練機からでた粘土の板を、正寸にカットする前に粗く切り分けたもの。これぞ粘土!という感じですね。
土練機では、成形するのにちょうどいい硬さになるまで、水を少しずつ加えながら練り合わせ、粘土の水分量を調整していきます。この時空気が混ざらないように真空状態で練り合わせ、練った粘土から空気をしっかり抜いて、板状に粘土を押し出します。
今回作っているのは100角タイル。
焼き上がりは97mmを目指し、素地は109.5mmにカットします。
湿式製法のタイルは含水率が高いので、焼成による収縮率が乾式製法のものより大きくなります。
土練機から出た粘土を、まずはざっと切り分けます。
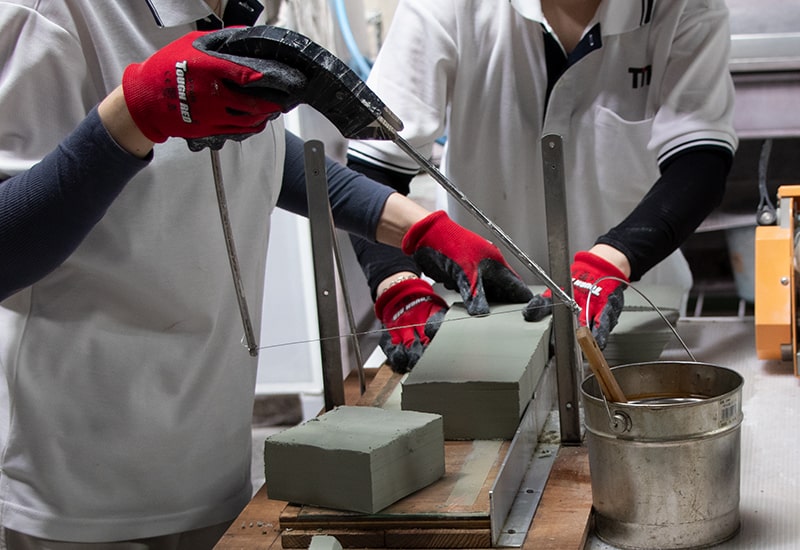
だいたいの大きさに切り分けたら、手動のタタラ成形機で整えていきます。
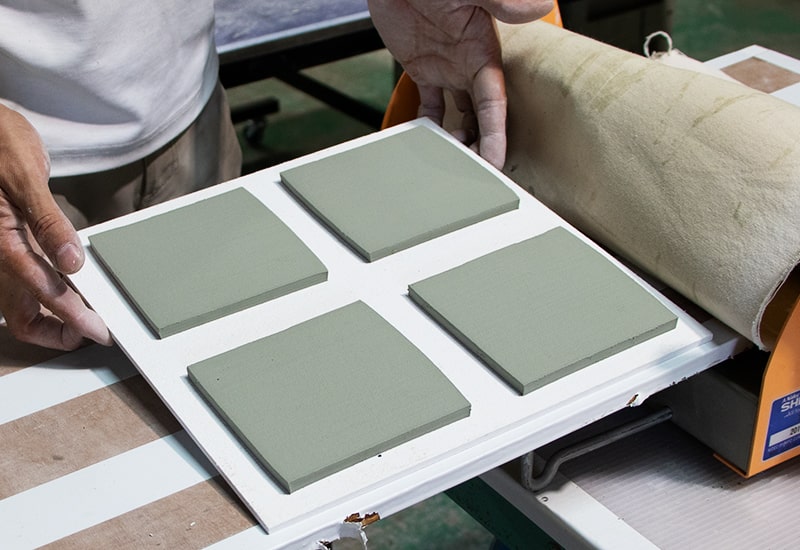
2本の回転するローラーの間に、必要な厚みよりも厚い粘土を通し、表面をならしつつ厚みも均一にしていきます。
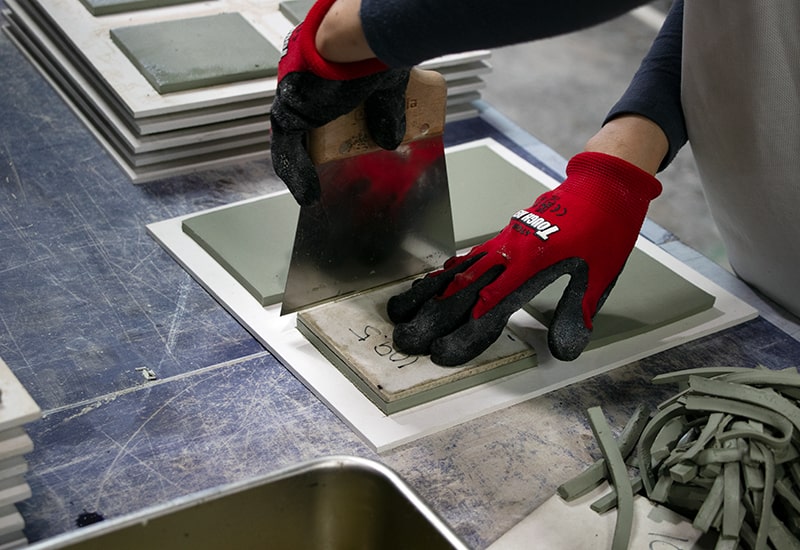
この後、109.5mmの型紙を使って、四隅を切り落とします。
何枚も何枚も、手作業なので大変です。
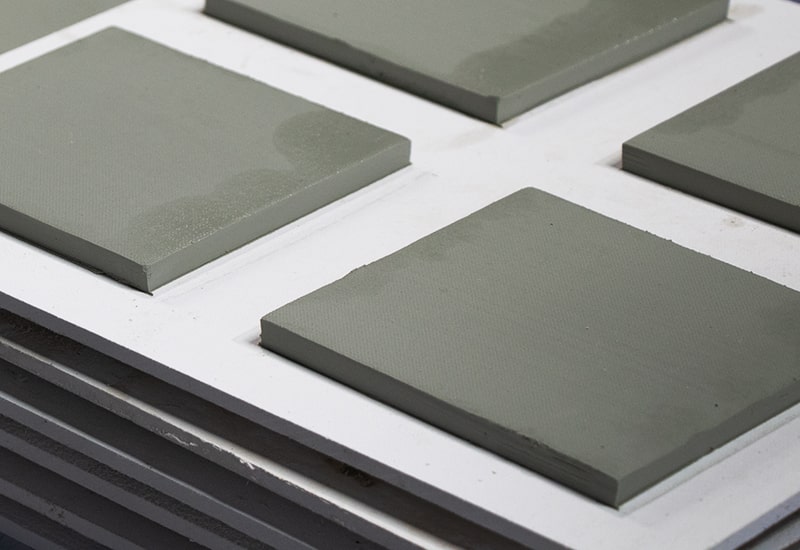
画像ではわかりにくいのですが、少し布目のついた素地ができました。さきほどの手動でくるくると回して使っていた、タタラ成形機でタイルに被せていた布の跡です。
この湿式タイル、まだまだこの後に表面加工の工程が続きます…。一枚一枚、非常に手間のかかるタイルです。
担当のスタッフが協力し、 試行錯誤しながらがんばっています。
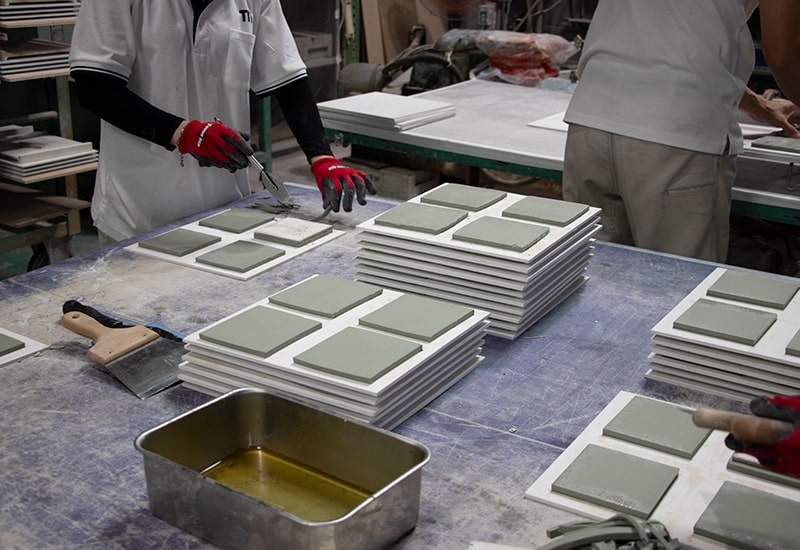
わたしたちの工場をはじめ、数多くのタイルメーカーが集まるこの地域。ですが、かつてたくさんあった湿式タイルを生産する工場は減少。
そんな状況の中、この土練機、 実は今年に入ってから新たに入れた設備なのです。
粘土を成形して、焼き固める。
昔からあるシンプルな製造方法である湿式製法には、土の持つ魅力がいっぱい。
大量生産ラインでは生み出せない「人の手の温もり」と「素材そのものの美しさ」を表現することができます。
今では、3メートルも超えるようなとても大きな、しかも薄い、そんなタイルがどんどん増えています。ダイナミックで美しい見た目、それに加え耐久性やメンテナンス性にも優れ、ホテルや、商業施設、オフィスビルなど、需要も多い。
確かにかっこいい。でも…
こんな時代の風潮の中ではありますが、 一枚一枚に味のある風合い豊かなタイルが、もっと身近にあるような、そんな空間が求められてもいいのでは、と感じます。
実際にタイルが焼き上がってくる現場を見ていただけると、その魅力を見出すきっかけがたくさんあるかと思います。
▼ 「タイルづくりの現場から」
過去のブログをまとめました!タイルはどんな風に作られていくのか。
成形、施釉、焼成… それ以外も?!
ぜひご覧ください。
https://tile-park.com/index.php/blog/detail/31422
この記事の執筆者:吉田(タイルパークスタッフ)
カタログやコンテンツ記事などの各種広報物作成を担当。出版・制作会社を経て、転居を機にタイル業界へ。タイルの魅力を模索中。
■関連商品のご紹介■
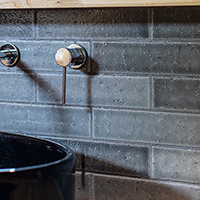
ダンボ
240×60サイズの湿式製法のタイル。
白とグレーの2色。 濃淡をつけたミックスになっています。
その色幅がなんともかわいい!
→「ダンボ」を見る
■おすすめサービス■