こんにちは、タイルパークの金谷です。
今回タイルのお話ではありませんが、9月に福岡のしっくいメーカー・田川産業株式会社さんの工場を見学する機会をいただき訪問してきましたので、その様子をお伝えします。
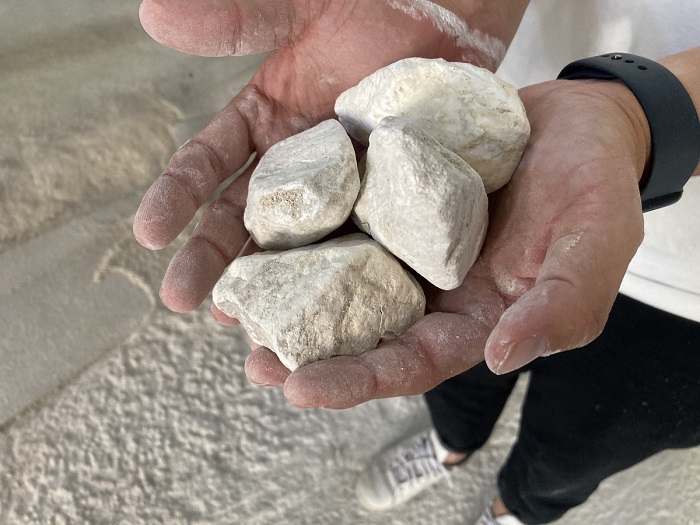
田川産業さんは福岡県田川市のしっくいメーカー。創業は1924年(大正13年)、なんと来年で創業から100周年を迎えられます。
筑豊地方で採掘される上質な石灰石と伝統の製法による良質な消石灰づくり、それを用いての革新的なアイデアによるエコロジカルな建築製品づくりが高く評価され、これまでグッドデザイン賞や福岡県産業デザイン賞など様々な賞に輝いています。
しっくいができるまで
今回は工場の様子を見ながら、実際のしっくい製造の流れをご説明いただきました。
はじまりは田川産業さんの工場からも見える筑豊地方の石灰採掘の山々。田川産業さんでは複数の山で採掘された石灰石をブレンドしています。
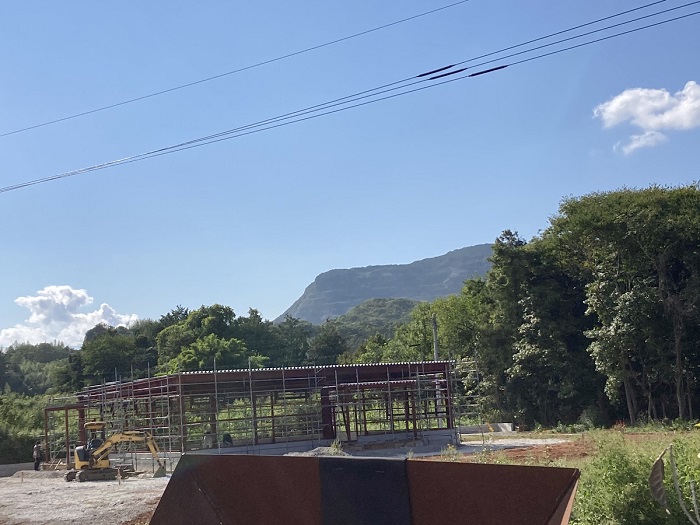
遠くに見える山が採掘山。石灰の採掘によって上の方が平らな段々畑のようになっています。
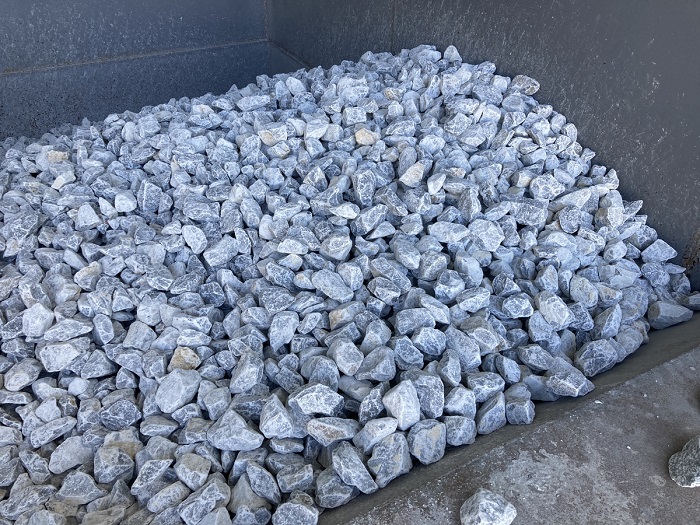
こちらが主原料となる石灰石。採掘時はこのようにグレーの石ですが、これを加熱焼成することで真っ白になります。
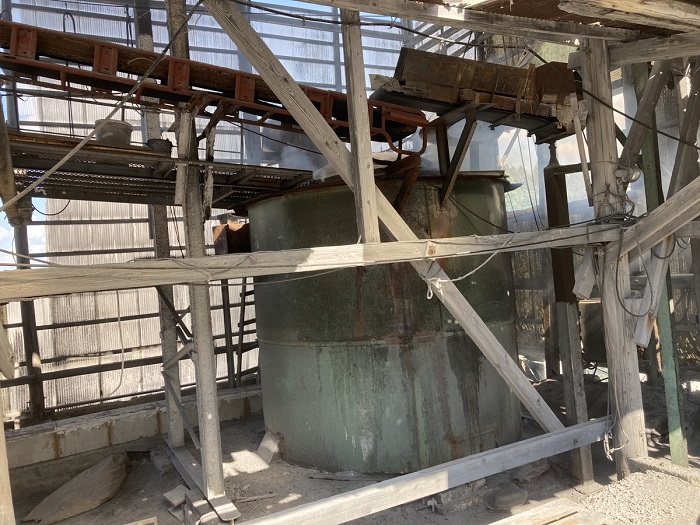
ブレンドされた石灰石はコークスと一緒に窯の中に運ばれて行き、「生石灰(酸化カルシウム)」に変化。この窯での焼成の際に塩を入れるのが「塩焼き」と呼ばれる製法です。不純物などを取り除き生石灰の質を高める重要なポイントで、しっくいづくりには欠かせない工程ですが、じつは全国に消石灰工場は多々あれど、「塩焼き」をおこなえる工場はほとんどないそうです。
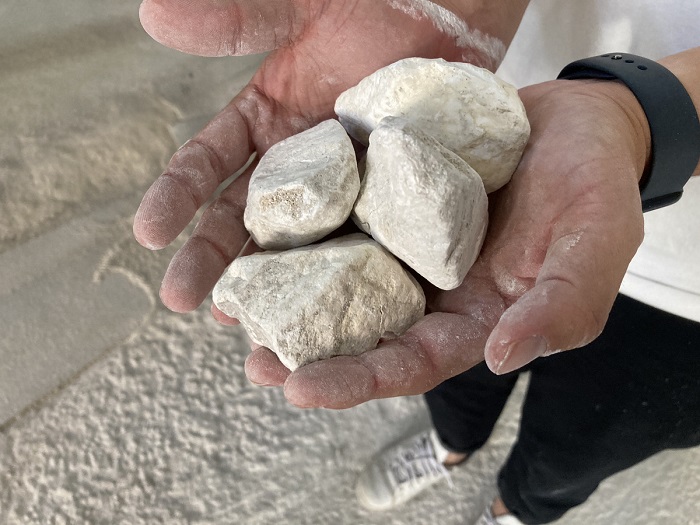
こちらが焼成を経た生石灰。先ほどのグレーの石灰石の状態からかなり色が変わっています。
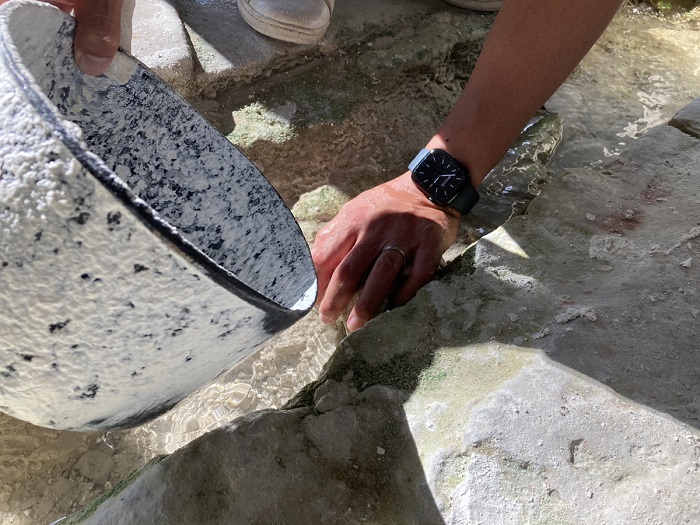
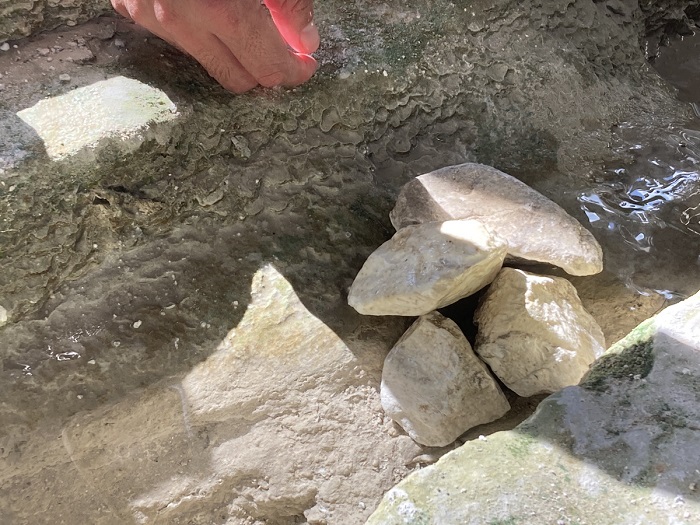
「ここからが見ものですよ」と、生石灰に水をかけ始めました。「消化」と呼ばれる工程です。生石灰が水によって化学反応を起こし、高熱を放出しながらむくむくと膨張していきます。しばらく見守っていると…
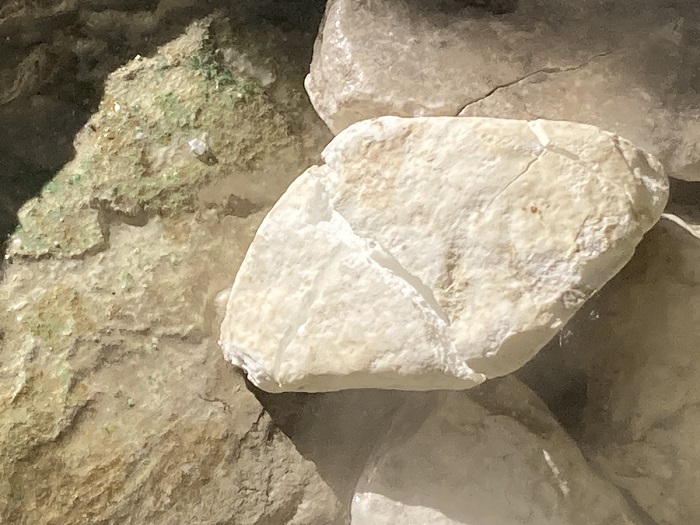
高温の蒸気を立ち昇らせながら、生石灰にひびが!
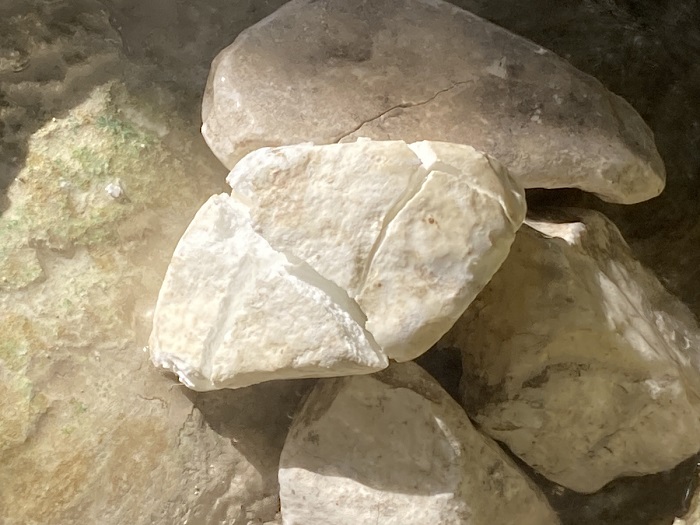
その後もあたりを真っ白な蒸気で覆いながら消化がどんどん進み・・・
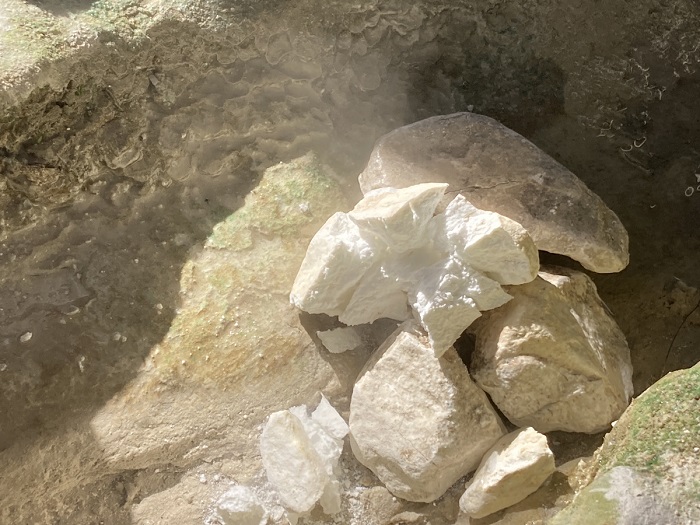
パカッ!
消化による膨張が進んで、とうとう生石灰が崩壊しました。中は真っ白で美しいです。
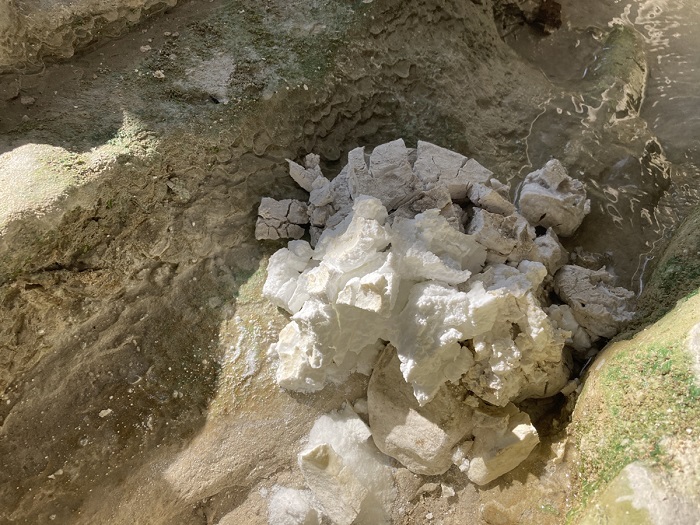
ついにはバラバラに…。こうしてできるのが「消石灰」。この粉末に増粘成分や繊維を加えることでしっくいが誕生します。
田川産業さんでは消化が不十分なものが混ざらないよう、しっかり人の手で選別をしてからしっくい製品や、この後ご紹介する「不焼成しっくいセラミック(=ライミックス)」に仕上げています。とくにライミックスは不十分な消化が混入すると硬化中に割れが起こりやすく、原料の品質が担保されていなければ作れない製品なのだそうです。
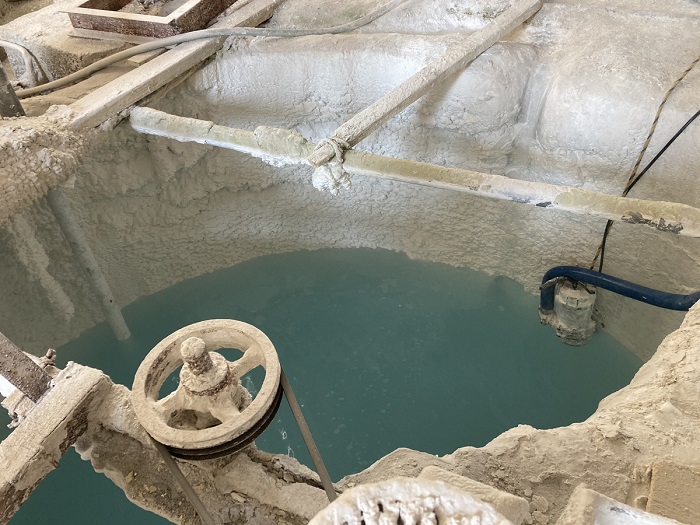
こちらは工場の中にあるタンク。カルシウム成分で真っ白になったタンクの水は、光を透過してサンゴ礁の海のように真っ青になります。トルコの有名な「パムッカレ」と同じ景色がこんなところにも!
なかなか見ることのできない工場の様子に大興奮。貴重な体験をありがとうございました。
環境にやさしい「しっくい」と、焼かないタイル「ライミックス」
しっくいは原料のほとんどが生物由来。天然の石灰岩はサンゴや貝、藻などの生物が堆積して出来たもので、これを加熱して生石灰にし、水で消化した「消石灰」に海藻などを抽出してつくるのりや繊維を加えることでしっくいになります。(ちなみに、今では当たり前の「水を加えるだけで使える既調合しっくい」も田川産業さんが日本で初めて発売したのだそう!)調湿や抗菌、消臭、硬化の過程で二酸化炭素を吸収するなど人にも環境にもやさしい建築素材です。
そして田川産業さんでは伝統製法で作られるこのしっくいを使い、不焼成セラミックタイル「ライミックス」を製造しています。
しっくいの塗り壁の場合は時間をかけて空気中の二酸化炭素を吸収して硬化しますが、ライミックスはしっくいの粉末をプレスでギュッとかため、石灰の加熱焼成時に発生したCO2を吸収させることで硬化するという見事なサイクルを実現。
大理石と同じように1枚ずつ施工できる強度を持ちながら、製造過程におけるCO2の排出を大幅に削減した環境負荷の少ないタイルとして、 グッドデザイン賞/中小企業庁長官賞など様々な賞を獲得しています。
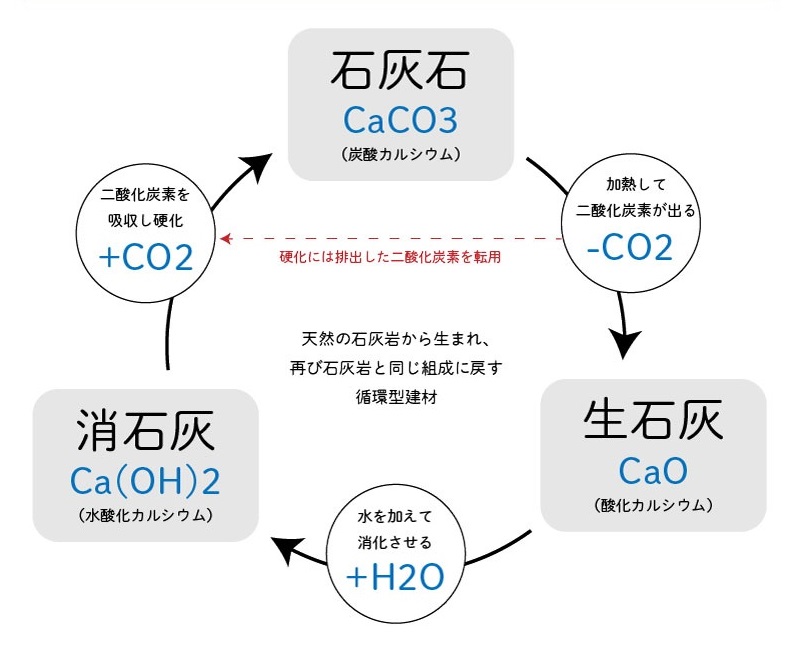
「しっくいを押し固め、排出した二酸化炭素を吸収させて硬化する」。言葉で書くとそのフローはシンプルではありますが、原料の質が悪いと均一に硬化させることができないなど、実際には大変高度な技術を要します。
行われるところがほとんどない伝統の製法「塩焼き」や、天然の素材へのこだわり、人の手を何度も介して選別をおこなう品質精度の高さを誇る田川産業さんだからできる製品「ライミックス」。革新的なものを生み出せるのは、それまで大切に守り続けてきた土台を持つ人たちなのだと実感します。